Get to know SafeClean
SafeClean extend the longevity and productivity of processing equipment and enables the systems to run on optimal flow for longer.
Chemical cleaning – for twenty years
In 2004, following an agreement with Statoil ( Equinor), SafeClean was challenged to remove deposits from two compact heat exchangers. Several competitors had tried on various occasions but had all failed.
Initially, Statoil had given up on cleaning these exchangers but allowed SafeClean the opportunity to demonstrate their capabilities. Using proprietary chemicals, SafeClean undertook the task. The exchangers were restored to nearly new condition in terms of cleanliness. The results were quantified by Heatric at Statoil's request.
Statoil became an important partner in the following years, and SafeClean became part of the energy company's supplier development program. Norsk Hydro also became a partner, and within a few years, SafeClean had built a solid equipment portfolio, obtained necessary certifications, and had a steadily increasing workload.
Statoil continually presented SafeClean with new challenges, and as early as 2007, SafeClean was tasked with circulating the entire process system on the Oseberg C platform during a maintenance shutdown. A task SafeClean has performed with success multiple times since then. In parallell to the development of a unique and comprehensive understanding of oil and gas processing systems, the company now offer a all-in-one contract for processing system cleaning to land fill waste handling.
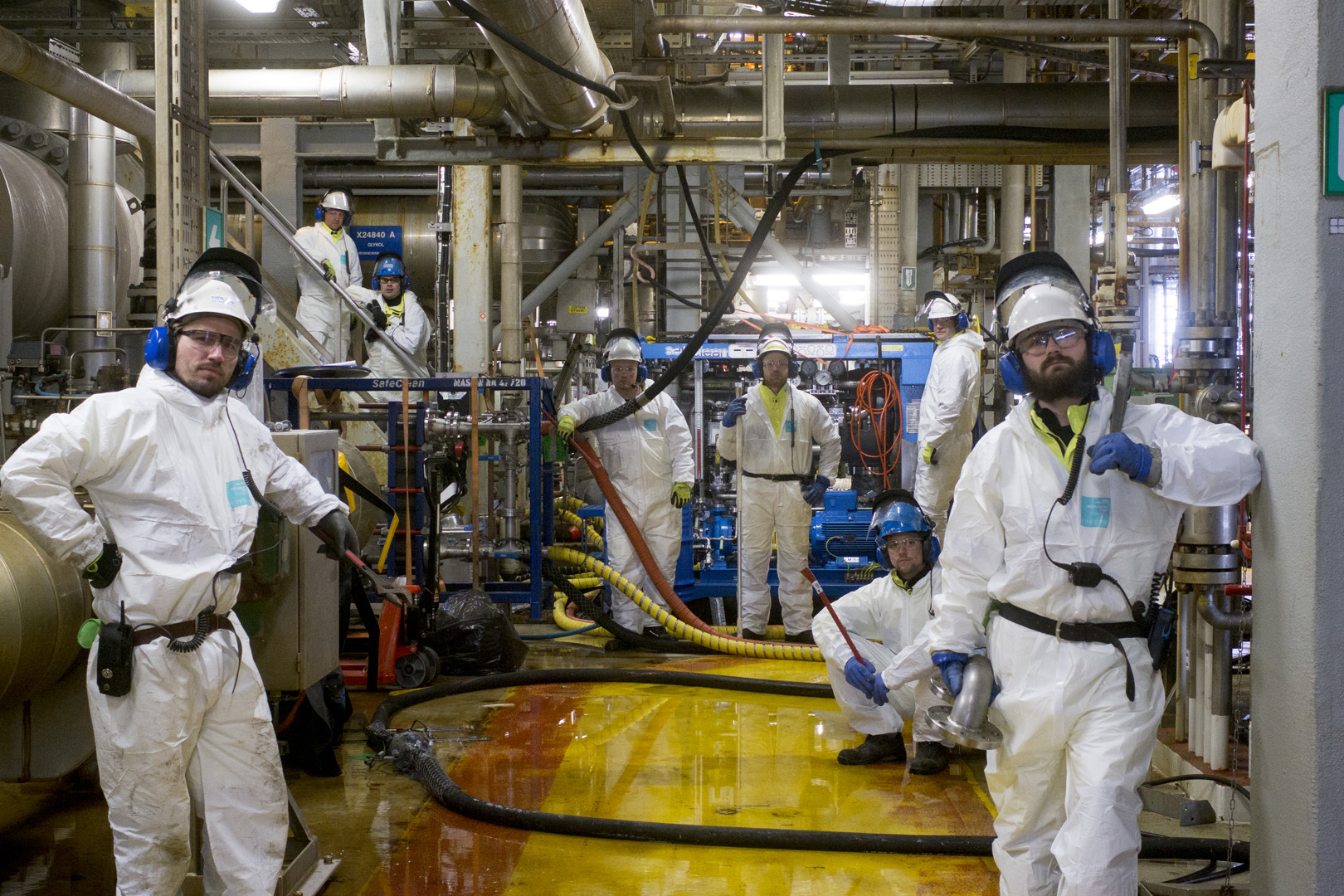